Il controllo statistico di processo nella produzione di circuiti stampati
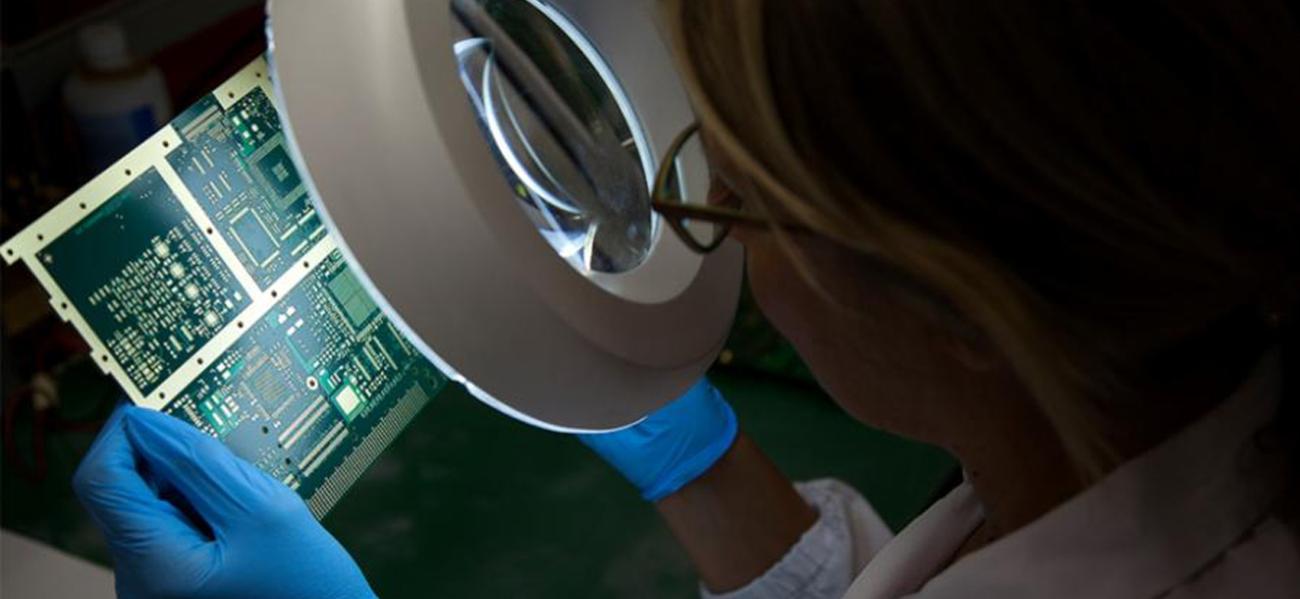
La qualità nasce come controllo metrologico del prodotto e questo concetto si sviluppa negli anni '90 come punto base delle prime versioni dello standard certificabile ISO 9001.
Nel tempo, però, gli standard hanno indicato l'opportunità non solo economica di diminuire il livello di controllo qualità, inteso come “autopsia di pezzi fuori tolleranza”, implementando una serie di logiche che spostano il focus dal prodotto al processo, con un approccio di tipo preventivo rispetto al momento produttivo.
Cistelaier ha adottato il controllo statistico delle variabili di processo da diversi anni e il laboratorio interno monitora costantemente l’andamento dei principali valori attraverso oltre 60 analisi di processo di cui sono noti gli andamenti e i valori storici di capacità.
Questa logica, similare a quella utilizzata per la validazione dei processi speciali (i.e. processi per cui non sono direttamente misurabili i risultati del processo), si avvale di forme di statistica più avanzate rispetto a quelle del controllo qualità classico, incentrate sulla verifica della capacità del processo, intesa come espressione statistica del livello dell’output rispetto alla tolleranza massima richiesta dalle specifiche di un prodotto.
Gli studi si basano sulla distribuzione normale, o di Gauss, per verificare se i valori del campione misurato, applicando l'ipotesi di normalità degli stessi, rappresentino una curva di processo compatibile con il campo di tolleranza atteso per tale valore.
In questo modo, a differenza dalla misurazione classica, che determina se una serie di valori si trovi, o meno, all'interno della tolleranza data, il sistema sarà in grado di esprimere la probabilità con cui i valori del processo ricadranno all'interno degli estremi di tolleranza e di prevedere l’eventuale percentuale di prodotti non conformi ad essa.
Addentrandoci nel campo della statistica, pur volendo mantenere un approccio divulgativo, possiamo dire che gli indici che rappresentano e descrivono questi comportamenti sono, in particolare il Cp e il Cpk.
Descrittivamente, possiamo definire che il Cp descrive la larghezza della Gaussiana attorno al valore medio, mentre che il Cpk rappresenti la centratura del processo rispetto agli estremi, essendo sempre Cpk ≤ Cp.
Nel seguente esempio, sono rappresentate due serie di valori di 25 misure su un target teorico di 1.5 ±0.1.
E’ possibile vedere come le due serie di valori, pur avendo entrambe il 100% delle misurazioni entro la tolleranza, evidenzino capacità di processo diverse rispetto alla misura attesa e come, per la seconda, sia prevedibile una percentuale di pezzi scarto.
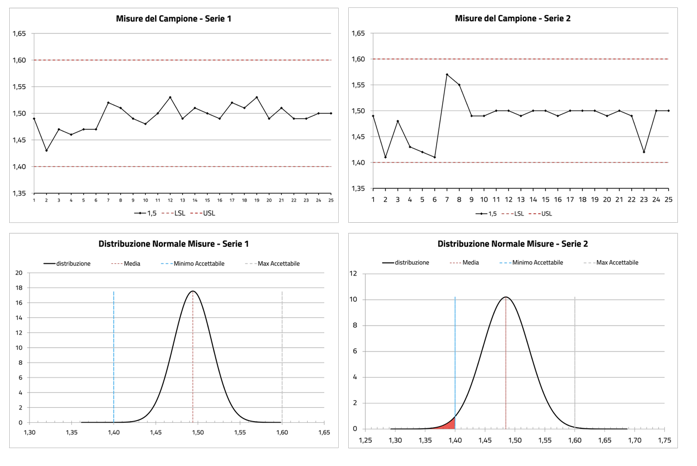
Si può osservare come gli indici di capacità delle due Serie siano diversi:
Serie 1 | Serie 2 |
Cp e Cpk > 1,33 | Cp e Cpk < 1 |
% Scarto attesa 0% | % scarto attesa 2% |
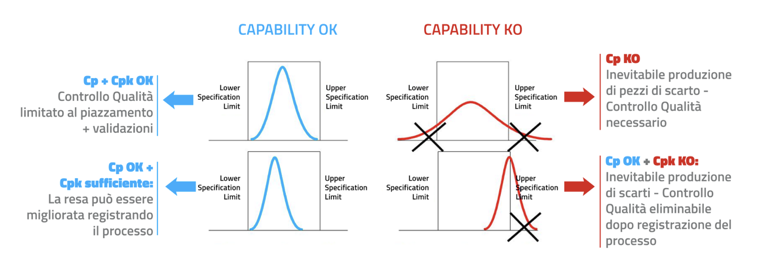
La conoscenza e l’interpretazione di questi valori permette di organizzare al meglio le frequenze di controllo qualità e di comprendere perché non sia possibile evitare alcune fasi di controllo al 100% durante la produzione dei circuiti stampati (in particolare il controllo ottico automatico dei lati interni e il test elettrico).
Sulla base dell'analisi di processo, si possono riscontrare differenti casistiche:
Tali condizioni determinano interventi differenziati per riportare il processo nelle condizioni ottimali.