L'umidità, un importante agente di rischio per i circuiti stampati
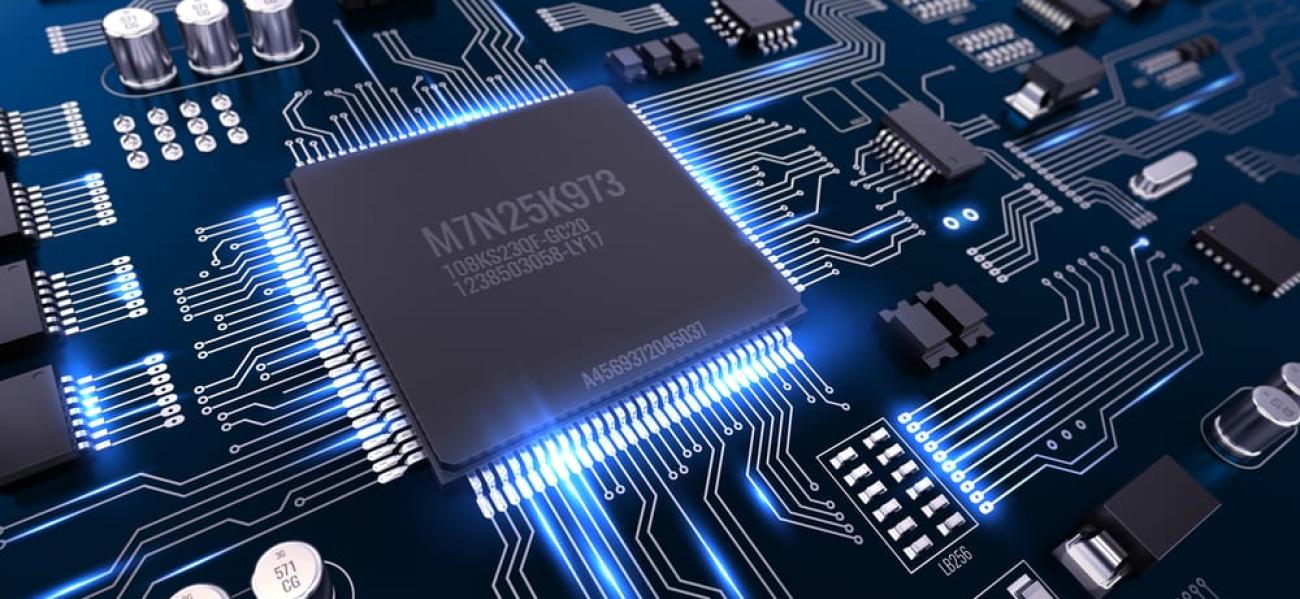
La regolamentazione RoHS del 2006 ha obbligato, salvo alcune eccezioni, alla sostituzione delle paste saldanti a base Piombo con paste saldanti senza Piombo, Lead free per l’appunto.
Fatte salve alcune eccezioni, come quelle relative alle applicazioni per la Difesa, per lo Spazio e per le parti security in ambito Automotive, le paste saldanti Lead free si sono sostituite a quelle a base Piombo per la saldatura dei componenti elettronici sui circuiti stampati.
Questo passaggio ha comportato un incremento delle temperature nei profili di saldatura di circa 30-40°C che ha prodotto effetti fino ad allora secondari o di poca rilevanza sulla conformità dei PCB e dei PCBA, come quello dovuto alla evaporazione dell’umidità.
I materiali di base standard sono costituiti da tessuti in fibra di vetro (trama e ordito) pre-impregnati da resina epossidica. Quest’ultima rende il materiale di base altamente igroscopico, cioè capace di assorbire l’umidità dall’ambiente che lo circonda.
La presenza dell’umidità all’interno delle schede è diventato un aspetto preponderante con il passaggio da lega Stagno-Piombo a lega Lead free.
Come si può vedere nella rappresentazione qui di seguito, l’umidità, sottoforma di micro-particelle di vapore acqueo, si insinua tra le fibre di vetro all’interno della resina epossidica.
Se questa condizione non creava particolari problemi in passato, con l’avvento della tecnologia Lead free ha invece portato alla luce molteplici criticità.
Come si può vedere dal grafico sottostante, la pressione che si crea durante il processo di assemblaggio in caso di umidità all’interno della scheda, cresce dai 400psi in caso di saldatura con paste Stagno-Piombo fino a 600psi in caso di saldatura con paste Lead free.
L’incremento di temperatura ha comportato un aumento di pressione all’interno delle schede durante la fase di saldatura.
La presenza di umidità nel PCB in fase di saldatura dei componenti elettronici può generare il fenomeno della Delaminazione, una delle più importanti difettosità per i PCB.
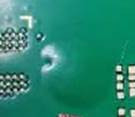
La delaminazione si genera durante la fase di assemblaggio dei componenti elettronici, nel momento in cui il circuito stampato viene sottoposto alle temperature di saldatura, e consiste nella separazione dei materiali di base che compongono lo stesso circuito stampato. Per questo motivo si manifesta per lo più come un evidente rigonfiamento superficiale.
Questo fenomeno compromette la funzionalità del PCB per effetto della riduzione dell’isolamento tra gli strati o, se in prossimità di forature, per effetto della frattura del foro metallizzato, vias o PTH che sia.
Un aspetto importante da considerare è quello della configurazione del circuito stampato e delle sue caratteristiche costruttive.
Ad esempio, la tecnologia di trattamento dei vias Type VII secondo IPC 4761, prevede il riempimento dei vias con resina termo conduttiva.
La resina utilizzata per tale scopo è altamente igroscopica e rappresenta pertanto un volume in cui l’umidità può intrappolarsi per poi fuoriuscire durante la fase di saldatura dei componenti elettronici creando delaminazione, come mostrano le immagini qui sopra.
Per questo motivo, il ricondizionamento in forno dei PCB è determinante per prevenire problematiche che possono pregiudicarne la conformità.
Oltre a difetti, come quello della delaminazione, che possono manifestarsi su un PCB durante l’assemblaggio, l’umidità influisce anche sul buon esito della finitura superficiale: l’umidità può infatti ossidare la superficie del rame esposto riducendone così la bagnabilità.
Nel prossimo articolo vedremo altre problematiche relative all’umidità e le tecniche di preservazione suggerite dallo standard internazionale IPC 1601.