Preparazione degli inner layer prima della pressatura
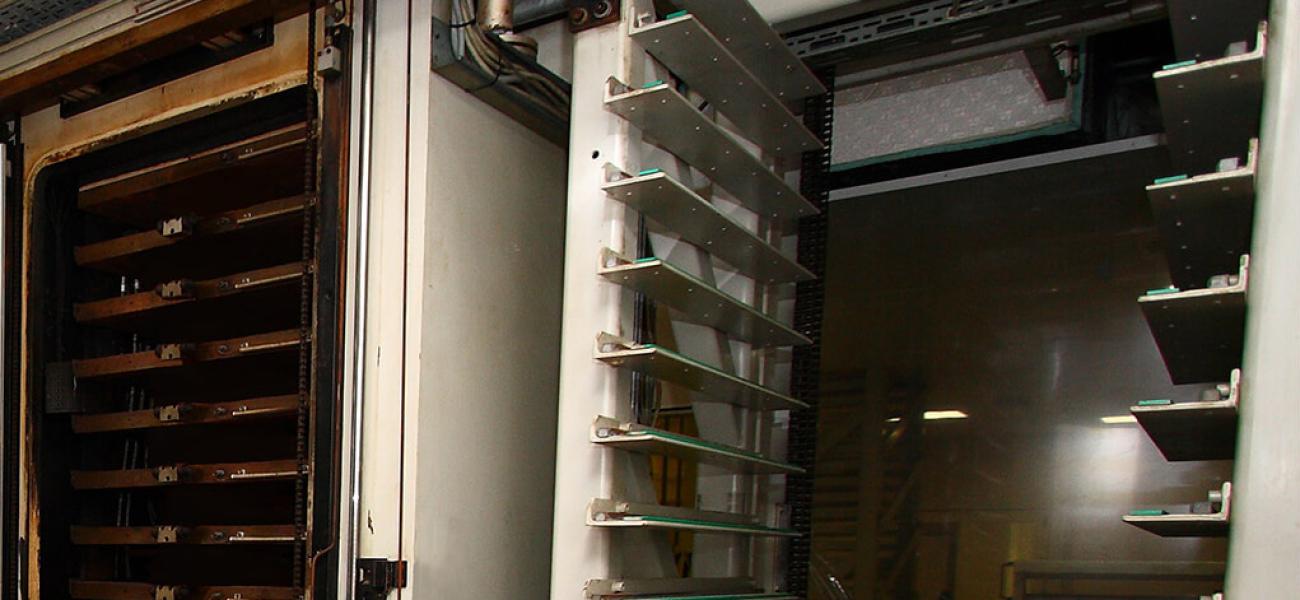
Eccoci di nuovo qui per continuare il nostro tour virtuale della fabbrica per comprendere meglio tutte le fasi necessarie per produrre un circuito stampato.
Dopo l'ispezione ottica automatica (AOI) degli inner layer, gli strati interni sono soggetti a:
- punzonatura;
- preparazione della superficie in rame.
Gli strati interni sono punzonati per ottenere i fori di registrazione necessari a garantire che siano allineati tra loro dopo la pressatura. L'operatore carica ogni inner nella punzonatrice che, tramite un sistema ottico, allinea l'inner layer stesso e lo punzona realizzando così i fori di registrazione.
Gli inner layer vengono stampati con una distorsione "predittiva" rispetto ai valori nominali: durante la fase di pressatura, infatti, gli strati interni cambiano leggermente le loro dimensioni a causa della temperatura e della pressione e in funzione principalmente del materiale di base e della percentuale di rame; questi cambiamenti vanno gestiti: si lavora a livello di micron, la "previsione" non può essere fatta "un tanto al braccio", le distorsioni di stampa si basano su anni e anni di esperienza.
Anche la forma dei fori di registrazione è importante per evitare qualsiasi rotazione degli inner layer tra loro durante la fase di pressatura.
Come abbiamo già detto, la produzione di PCB richiede un'ampia gamma di competenze in cui chimica e meccanica sono spesso mescolate.
Dopo la punzonatura, gli inner sono pronti per la preparazione della superficie del rame prima della pressatura.
L'obiettivo principale di questa fase è di rendere la superficie del rame sufficientemente "ruvida" da garantire la migliore adesione possibile con il pre-preg durante la pressatura, in modo da evitare uno dei rischi più critici nei PCB: la delaminazione.
La preparazione del rame avviene attraverso un processo chimico tipicamente chiamato black-oxide: si basa infatti sull'ossidazione della superficie del rame che cambia aspetto passando da brillante ad annerita. A questa variazione corrisponde l’acquisizione della rugosità da parte della superficie di rame.
Un'ulteriore fase per evitare il rischio di delaminazione è quella di effettuare sugli strati interni un baking dopo il processo di black-oxide. Questo processo termico garantisce l'evacuazione dell'umidità dagli inner layer.
La vaporizzazione dell'umidità durante la pressatura potrebbe essere responsabile della mancata adesione della resina del pre-preg con gli strati interni o con la lamina di rame, il copper foil, su cui verranno “disegnati” gli strati esterni.
La delaminazione potrebbe mostrare la sua presenza più tardi, dopo la pressatura, sotto forma di "bolle" sotto il copper foil o ancora più tardi dopo l'incisione degli strati esterni con conseguenti "macchie o chiazze biancastre" sulla superficie del PCB; o, ancora, sotto forma di pink ring, una delaminazione locale alla interfaccia inner layer – foro, che diventa evidente dopo la dissoluzione dell'ossido di annerimento durante i processi di placcatura.
Ecco perché una corretta preparazione della superficie del rame unita all'assenza di umidità sono "un must" per evitare la delaminazione.
Se vuoi saperne di più sul processo di produzione dei PCB, non esitare a contattarci!